In metal eyewear manufacturing, surface treatment processes significantly impact the product’s appearance, durability, and market competitiveness. Electroplating and spray painting are two of the most widely used surface treatment techniques, each with its unique advantages and applications. Electroplating involves coating the metal surface with a thin layer of metal to enhance corrosion resistance and gloss, while spray painting applies paint to the metal surface, offering a wide range of color options and texture effects. This article will provide a detailed comparison of electroplating and spray painting in metal eyewear manufacturing, helping brands choose the best surface treatment method.
2. Overview of Electroplating Process
Basic Principles and Process of Electroplating
Electroplating is a process that uses electrochemical reactions to deposit a layer of metal or alloy on the surface of a metal. The basic steps include pre-treatment, electroplating, and post-treatment. During electroplating, the eyewear frame is immersed in an electrolyte solution and serves as the cathode. An electric current passes through the solution, causing metal ions to reduce and form a uniform, dense coating on the frame’s surface. Common electroplating materials include nickel, chrome, gold, and silver, each providing different appearances and properties to metal eyewear.
Common Applications of Electroplating in Metal Eyewear
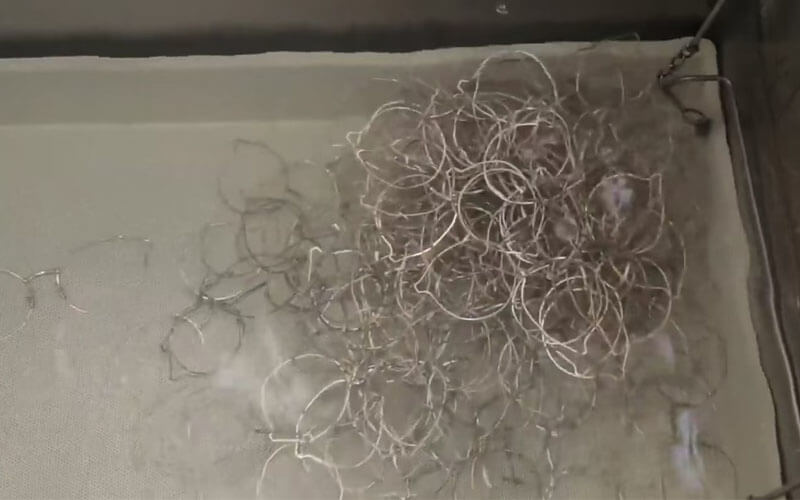
Electroplating is widely used in the manufacturing of high-end metal eyewear, known for its luster and corrosion resistance, allowing products to maintain a good appearance over long periods. In particular, gold and chrome plating are popular in the luxury market due to their luxurious feel and high durability. Electroplating is also commonly used as a base layer in eyewear frames to enhance the adhesion and durability of subsequent coatings.
-
Bulk Buy Metal Eyewear – 3062
$80.00 Select options This product has multiple variants. The options may be chosen on the product page -
Bulk Wholesale Circle Metal Eyewear – 18106
$99.00 Select options This product has multiple variants. The options may be chosen on the product page -
Bulk Wholesale Metal Eyewear – HT004
$80.00 Select options This product has multiple variants. The options may be chosen on the product page -
Buy Metal Eyewear in Bulk – 3096
$80.00 Select options This product has multiple variants. The options may be chosen on the product page
Advantages and Disadvantages of Electroplating
Advantages | Description |
Durability | Electroplated layers offer excellent wear and corrosion resistance, effectively extending the lifespan of metal eyewear. |
Corrosion Resistance | Electroplating effectively prevents the metal substrate from interacting with the environment, reducing oxidation and corrosion risks. |
Metallic Finish | Electroplating imparts a high gloss and metallic texture to eyewear, enhancing its premium feel and market appeal. |
Disadvantages | Description |
Higher Cost | The electroplating process is relatively complex and costly, especially when using precious metals like gold and platinum. |
Limited Color Options | Electroplating is usually limited to metallic colors like gold, silver, and chrome, making it difficult to achieve a wide range of color variations. |
Environmental Concerns | The electroplating process can generate hazardous waste and pollutants, requiring proper treatment to minimize environmental impact. |
3. Overview of Spray Painting Process
Basic Principles and Process of Spray Painting
Spray painting involves applying paint to the metal surface to create a coating. The spray painting process typically includes pre-treatment, spraying, and curing. Paint is sprayed evenly onto the metal eyewear frame using a spray gun, and the coating is then cured by baking or air-drying to ensure it adheres firmly to the metal surface. Spray painting is highly flexible and can achieve various color and texture effects, making it an essential technique for personalized designs.
Common Applications of Spray Painting in Metal Eyewear
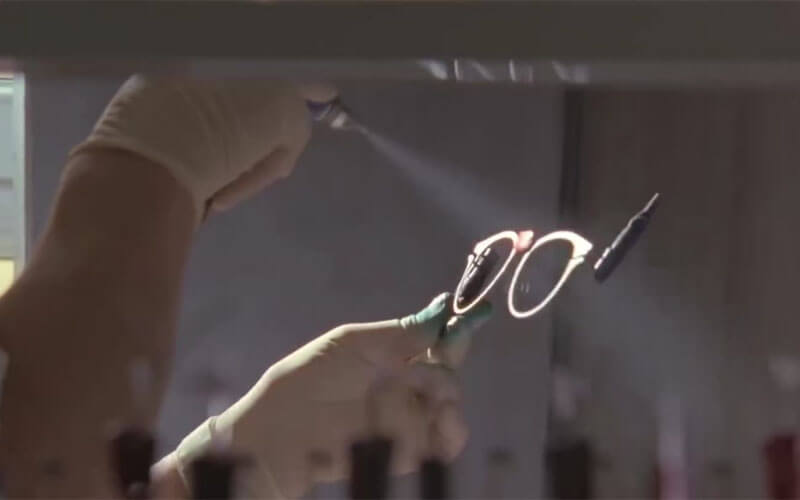
Spray painting is widely used in the production of fashion-forward and personalized eyewear, particularly for products with vibrant colors and strong design elements. The technique easily achieves gradient colors, matte, glossy, and other surface effects, meeting the diverse needs of consumers. Spray painting is also suitable for small-batch customized production, allowing brands to quickly adapt product designs according to market trends.
Advantages and Disadvantages of Spray Painting
Advantages | Description |
Wide Color Range | Spray painting can achieve almost limitless color options, from solid colors to gradients, from matte to glossy, meeting various design needs. |
Rich Texture | Spray painting adds a variety of texture effects to metal eyewear, such as soft matte, smooth gloss, and unique textures, giving products more personality. |
High Flexibility | Spray painting is easy to adjust and operate, making it suitable for small-batch production and quick market response. |
Disadvantages | Description |
Lower Durability | Compared to electroplating, spray-painted coatings are less wear-resistant and may peel or fade after long-term use. |
Adhesion Challenges | The adhesion of spray-painted coatings depends on the quality of the pre-treatment, and if not properly handled, the coating may peel off. |
Environmental Impact | Traditional spray painting uses solvent-based paints that may release VOCs, impacting the environment. Eco-friendly paints are needed to reduce pollution. |
4. Electroplating vs. Spray Painting: Aesthetic Comparison
Color Performance and Saturation
In terms of color performance, spray painting has a clear advantage. Spray painting can achieve a wide variety of vibrant colors and complex gradients, with high color saturation, making it ideal for fashion-forward and personalized product designs. In contrast, electroplating is generally limited to metallic colors, offering fewer color options and being more suitable for high-end and classic products.
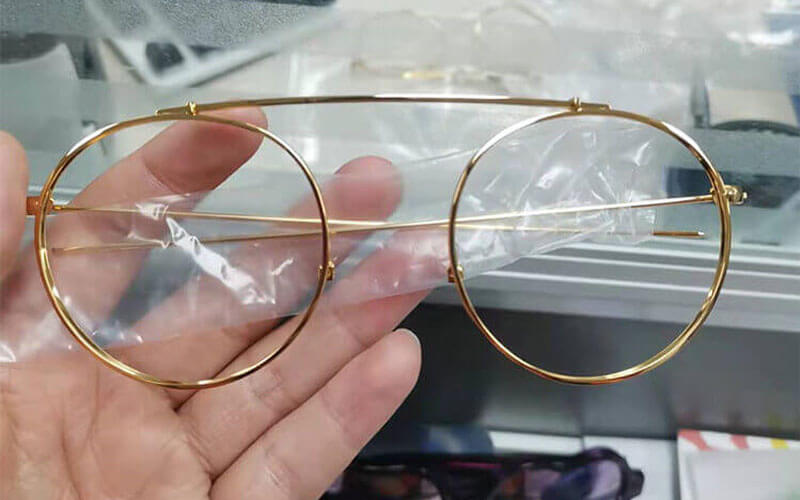
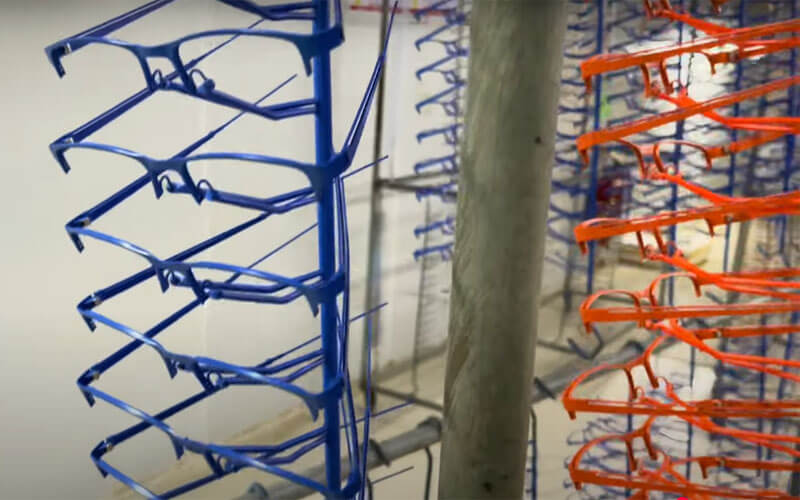
Surface Gloss and Texture
Electroplating excels in surface gloss and metallic texture, particularly with chrome and gold plating, giving products a mirror-like shine and a luxurious feel. On the other hand, spray painting offers a broader range of texture effects, including matte, silky, and glossy finishes, catering to different market and consumer preferences.
Texture Effects and Personalized Design
Spray painting can easily achieve various texture effects and personalized designs, such as wood grain, brushed effects, and more. These effects enrich the visual and tactile experience of the product. In comparison, electroplating is less effective at creating complex textures but still offers a unique market advantage with its consistent metallic finish.
Comparison Dimension | Electroplating | Spray Painting |
Color Options | Limited to metallic colors like gold, silver, and chrome | Can achieve vibrant colors and gradients |
Surface Gloss | Mirror-like gloss, high metallic texture | Can achieve matte, glossy, and silky textures |
Texture Effects | Limited texture effects, focuses on metallic finish | Can achieve complex textures like wood grain and brushed effects |
-
Buy Wholesale Metal Eyewear in Bulk – 2007
$80.00 Select options This product has multiple variants. The options may be chosen on the product page -
Metal Eyewear Wholesale Suppliers – TA001
$80.00 Select options This product has multiple variants. The options may be chosen on the product page -
Wholesale Highend Metal Eyewear – 1988
$99.00 Select options This product has multiple variants. The options may be chosen on the product page -
Wholesale Retro Metal Eyewear – 28634
$99.00 Select options This product has multiple variants. The options may be chosen on the product page
5. Electroplating vs. Spray Painting: Durability and Performance
Corrosion Resistance and Wear Resistance
Electroplating has a clear advantage in corrosion and wear resistance. In harsh environments, electroplated layers effectively prevent metal oxidation and wear, extending the product’s lifespan. Spray-painted coatings are relatively weaker in this regard, especially after long-term use, where coatings may wear out or peel off.
Coating Adhesion and Durability
Electroplated layers exhibit strong adhesion to the metal substrate, ensuring durability and long-term stability. In contrast, the adhesion of spray-painted coatings relies more on the quality of the pre-treatment; if not properly handled, the coating may peel off, affecting the product’s lifespan.
Real-world Performance and Durability Testing
In real-world use, electroplated eyewear typically demonstrates greater durability and longer service life, especially in outdoor and high-humidity environments where electroplating provides better protection against external damage. Spray-painted eyewear performs well in daily use but may not be as durable as electroplated eyewear under extreme conditions.
Performance Dimension | Electroplating | Spray Painting |
Corrosion Resistance | Strong, suitable for harsh environments | Relatively weaker, may degrade over time |
Wear Resistance | Strong wear resistance, suitable for long-term use | Relatively lower wear resistance, may wear over time |
Adhesion | Strong adhesion, stable and durable | Adhesion depends on pre-treatment, may peel off |
6. Electroplating vs. Spray Painting: Environmental and Health Considerations
Environmental Issues in Electroplating and Solutions
Traditional electroplating processes can generate hazardous wastewater and waste, impacting the environment, especially when using chromium or cyanide-based electroplating. To reduce environmental impact, modern electroplating processes are gradually shifting to cyanide-free and chromium-free electroplating, with wastewater recycling technologies to lower environmental pollution. Additionally, electroplating facilities usually need to comply with strict environmental regulations and certifications to ensure sustainable production.
VOC Emissions in Spray Painting and the Choice of Eco-friendly Paints
Spray painting processes using traditional solvent-based paints can release volatile organic compounds (VOCs), negatively impacting the environment and human health. To address this issue, eco-friendly water-based and low-VOC paints are becoming mainstream, significantly reducing harmful emissions and improving environmental sustainability. Advanced spraying equipment and ventilation systems also help control VOC emissions, protecting the environment and the health of operators.
Health Impact and Safety Standards Comparison
The safety of products is a key concern for consumers, whether electroplated or spray-painted. Nickel used in electroplating can cause allergic reactions in some individuals, so nickel-plated products must comply with international standards on nickel release limits. In spray painting, if the paint contains heavy metals or other harmful substances, it can also pose a risk to the wearer’s health. Therefore, manufacturers should choose eco-friendly materials that comply with RoHS directives and REACH regulations to ensure the final product is safe for wearers.
Environmental and Health Considerations | Electroplating | Spray Painting |
Environmental Issues | Generates hazardous wastewater, addressed by cyanide-free and chromium-free electroplating and wastewater recycling technologies | Releases VOCs, addressed by using eco-friendly water-based and low-VOC paints |
Health Impact | Nickel plating may cause allergic reactions, requires control of nickel release | Paint may contain heavy metals, requires use of eco-friendly materials compliant with RoHS and REACH |
7. Electroplating vs. Spray Painting: Cost and Production Efficiency
Production Costs and Complexity of Electroplating
The complexity of the electroplating process and strict environmental treatment requirements make it relatively expensive. In large-scale production, the investment and operating costs of electroplating equipment are significant. Additionally, the electroplating process requires multiple steps and strict quality control, increasing production complexity and time costs. However, for high-end products, the durability and high gloss of electroplating often justify the higher costs.
Cost Advantages of Spray Painting and Application in Small-batch Production
Spray painting is relatively simpler and less costly than electroplating, making it particularly suitable for small-batch production and quick market response. Spray painting equipment requires less investment and is easier to operate, allowing flexible adjustments in color and effect to suit different market trends. For brands that need to frequently launch new models, the lower cost and high flexibility of spray painting are significant advantages.
Efficiency and Cost Control in Large-scale Production
In large-scale production, electroplating has a high degree of automation, ensuring high production efficiency, but its environmental treatment and maintenance costs remain high. Spray painting, on the other hand, offers more flexible cost control in large-scale production, especially with the use of eco-friendly paints that can reduce the cost of VOC emissions treatment. Overall, spray painting has a more apparent cost advantage in large-scale production, but electroplating remains important in specific high-end markets.
Cost and Efficiency Comparison | Electroplating | Spray Painting |
Production Costs | Higher, especially in large-scale production | Lower, suitable for small-batch production and quick adjustments |
Process Complexity | Complex, requires strict quality control and environmental treatment | Relatively simple, flexible operation and easy adjustment |
Large-scale Production Efficiency | High automation, high efficiency, but higher environmental costs | Flexible cost control, eco-friendly paints reduce treatment costs |
8. Application Scenarios and Market Demand Analysis
Choosing Electroplating or Spray Painting Based on Product Positioning
Electroplating is suitable for high-end, classic metal eyewear, catering to markets that value luxury and durability. Gold and chrome plating are often used in the production of high-end business eyewear and luxury eyewear, meeting consumers’ high expectations for quality and value. Spray painting, on the other hand, is more suitable for fashion-forward, personalized product designs, allowing for quick adaptation to market trends and meeting young consumers’ diverse needs for color and texture.
Market Preferences for Different Surface Treatment Processes
High-end markets generally prefer electroplating because the gloss and durability it provides can elevate the product’s premium feel. In mid-range markets and among young consumers, spray painting is more popular due to its wide range of color options and personalized designs. Additionally, environmentally conscious markets tend to prefer products that use eco-friendly spray painting materials.
Choosing Electroplating or Spray Painting for Customization Needs
In customization scenarios, both electroplating and spray painting have their strengths. For customers seeking high-end finishes and metallic gloss, electroplating is the best choice; for those looking for bold innovations in color and texture, spray painting offers more options and design freedom. In small-batch customization, the flexibility and cost advantages of spray painting are more apparent, allowing for a quick response to customer needs.
Market and Customization Needs | Electroplating | Spray Painting |
High-end Market | Prefers electroplating for luxury and durability | Prefers spray painting for vibrant colors and rich textures |
Customization Needs | Focused on high-end finishes and metallic gloss | Focused on color and texture innovation, suitable for small-batch customization |
9. Conclusion and Recommendations
In metal eyewear manufacturing, both electroplating and spray painting have their unique advantages and applications. Electroplating, with its superior durability, corrosion resistance, and high gloss, is suitable for high-end, luxury products; spray painting, with its wide range of color options, diverse textures, and production flexibility, is more suited to the fashion-forward, personalized market. When choosing a surface treatment process, brands should consider product positioning, market demand, and cost-effectiveness. In the future, with ongoing technological advancements, electroplating and spray painting are expected to further innovate and merge, bringing more possibilities to metal eyewear design and production.
Here are some frequently asked questions (FAQs) related to the comparison between electroplating and spray painting in metal eyewear manufacturing:
1. What is the main difference between electroplating and spray painting in metal eyewear manufacturing?
Answer:
The main difference lies in the process and the effects they produce. Electroplating involves coating the metal surface with a thin layer of metal, enhancing durability, corrosion resistance, and providing a high-gloss, metallic finish. Spray painting, on the other hand, involves applying paint to the metal surface, offering a wide range of color options and texture effects, making it ideal for fashion-forward and personalized designs.
2. Which process is more durable: electroplating or spray painting?
Answer:
Electroplating is generally more durable than spray painting. It provides superior wear resistance, corrosion protection, and adhesion, making it ideal for products that require long-lasting performance, especially in harsh environments. Spray painting, while offering flexibility and color variety, may not be as durable over time, particularly in terms of wear and corrosion resistance.
3. Can both electroplating and spray painting be used on the same eyewear product?
Answer:
Yes, both processes can be used on the same eyewear product to achieve different effects. For example, electroplating can be used to create a durable, glossy metallic base layer, while spray painting can add color or texture on top of the electroplated surface, combining the strengths of both techniques.
4. How do electroplating and spray painting compare in terms of environmental impact?
Answer:
Electroplating can have a significant environmental impact due to the use of chemicals like chromium and cyanide, which require careful waste management to prevent pollution. Modern electroplating techniques are moving towards more eco-friendly processes, such as cyanide-free and chromium-free electroplating. Spray painting, particularly with traditional solvent-based paints, releases volatile organic compounds (VOCs), which can harm the environment and human health. The use of water-based and low-VOC paints in spray painting is becoming more common to reduce these impacts.
5. Which process offers more color variety and customization options?
Answer:
Spray painting offers more color variety and customization options than electroplating. It can produce almost any color, including complex gradients, matte, and glossy finishes, and can easily accommodate personalized designs. Electroplating is generally limited to metallic colors like gold, silver, and chrome, making it less flexible in terms of color customization.
6. What are the cost implications of choosing electroplating over spray painting?
Answer:
Electroplating tends to be more expensive than spray painting due to the complexity of the process, the cost of materials, and the need for environmental controls. The higher cost is often justified for high-end products that require superior durability and a premium finish. Spray painting is generally less expensive, especially for small-batch production, and offers more flexibility in terms of design and color changes, making it more cost-effective for fashion-focused and rapidly changing markets.
7. Is electroplating or spray painting better for small-batch or custom production?
Answer:
Spray painting is generally better suited for small-batch or custom production due to its flexibility, lower cost, and the ability to quickly adapt to different designs and colors. Electroplating, while offering superior durability and a luxurious finish, is more complex and expensive, making it less ideal for small-batch or frequently changing designs.
8. How do these processes affect the health and safety of eyewear users?
Answer:
Both processes must adhere to strict safety standards to ensure the health and safety of eyewear users. Electroplating can involve the use of nickel, which may cause allergic reactions in some individuals; therefore, nickel release must be controlled to comply with regulations. Spray painting, if not properly managed, could leave residues of harmful chemicals or heavy metals on the product, which can pose health risks. Manufacturers are increasingly using eco-friendly, compliant materials to minimize these risks.
9. Which process is more suitable for high-end luxury eyewear?
Answer:
Electroplating is more suitable for high-end luxury eyewear due to its ability to produce a high-gloss, durable, and metallic finish that exudes quality and luxury. It is ideal for products that need to maintain their premium appearance over time. While spray painting offers versatility in color and texture, electroplating provides the level of durability and sophistication typically associated with luxury items.
10. What future trends can we expect in the use of electroplating and spray painting in eyewear manufacturing?
Answer:
In the future, we can expect greater integration of eco-friendly technologies in both electroplating and spray painting. This includes the development of more sustainable electroplating processes that reduce environmental impact and the use of water-based, low-VOC paints in spray painting. Additionally, advances in smart manufacturing technologies may enhance the precision and efficiency of these processes, allowing for even more intricate designs and higher quality finishes.
Receive Custom Guidance
Looking for the perfect custom eyewear to represent your brand?
Reach out to Eyewearbeyond for expert guidance on choosing the best materials, styles, and customizations for your eyewear collection!